Selective Laser Sintering (SLS) 3D Printing
Selective Laser Sintering (SLS) is a commonly used powder-based additive technology to create models, prototypes and end-use parts in durable, engineering-grade thermoplastics. Consider SLS technology for applications that involve high-complexity and organic geometries, as well as parts requiring durability. SLS nests in the z direction which allows for short-run production and efficient builds. This technology is also capable of producing parts with finer details than most other additive processes that use high-strength plastics. The composition is one of the more isotropic available from additive manufacturing.
How does SLS Technology Work?
SLS uses a blade to spread a thin layer of powder over the build volume. A laser sinters the cross-section of the part to fuse the powder together. The z stage then drops one layer and the process begins again until the build is finished. Parts are then excavated from the build powder-cake so excess powder can be removed. The unused powder in the build envelope acts as the support structures which eliminates the need to remove support structures after the build process.
SLS 3D Printed Parts & Images / /
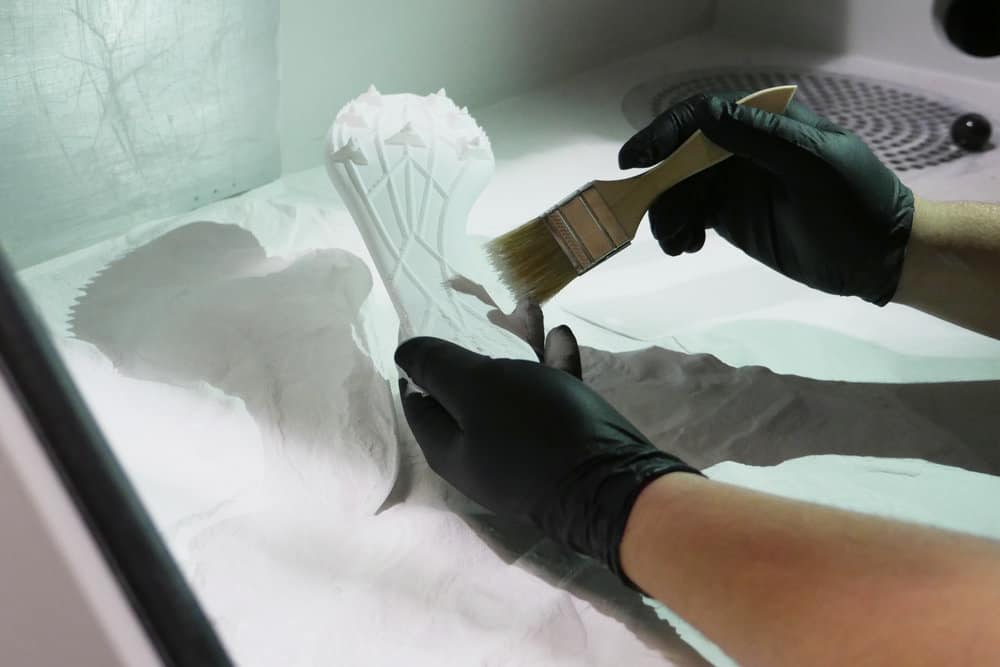
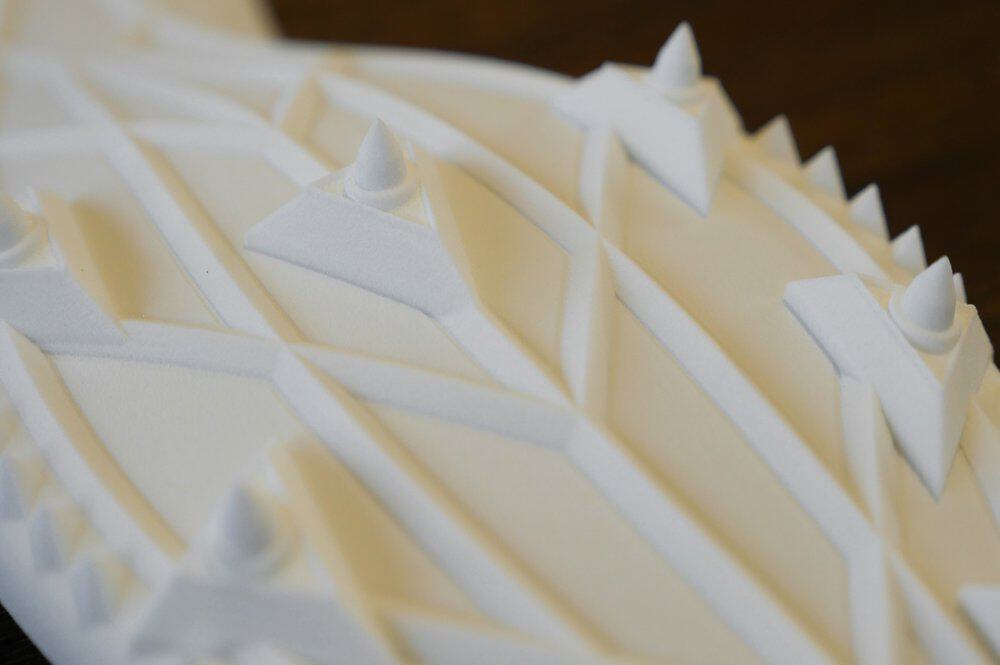
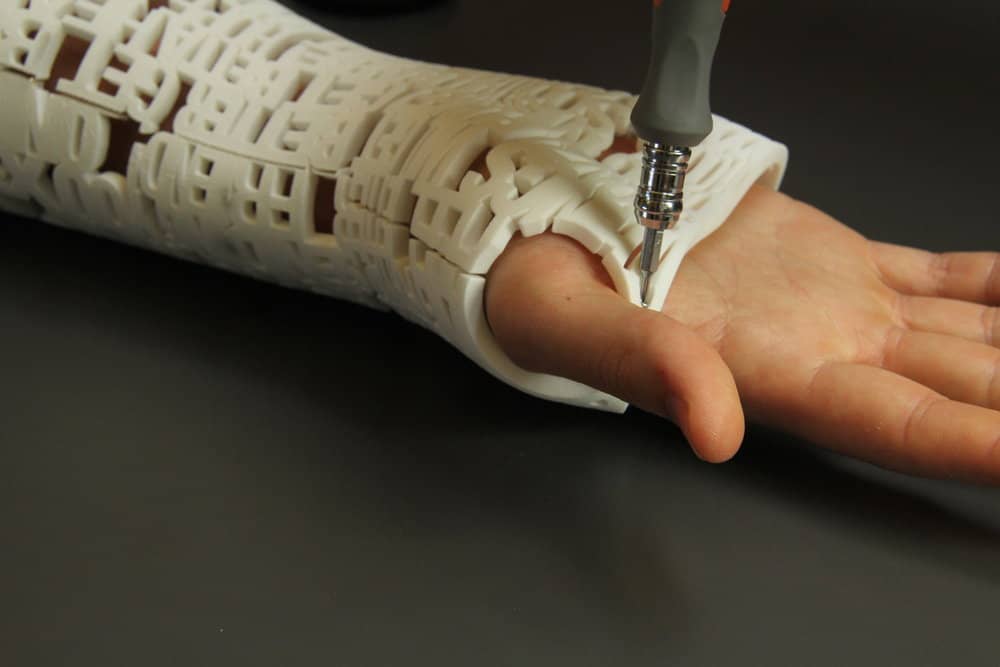
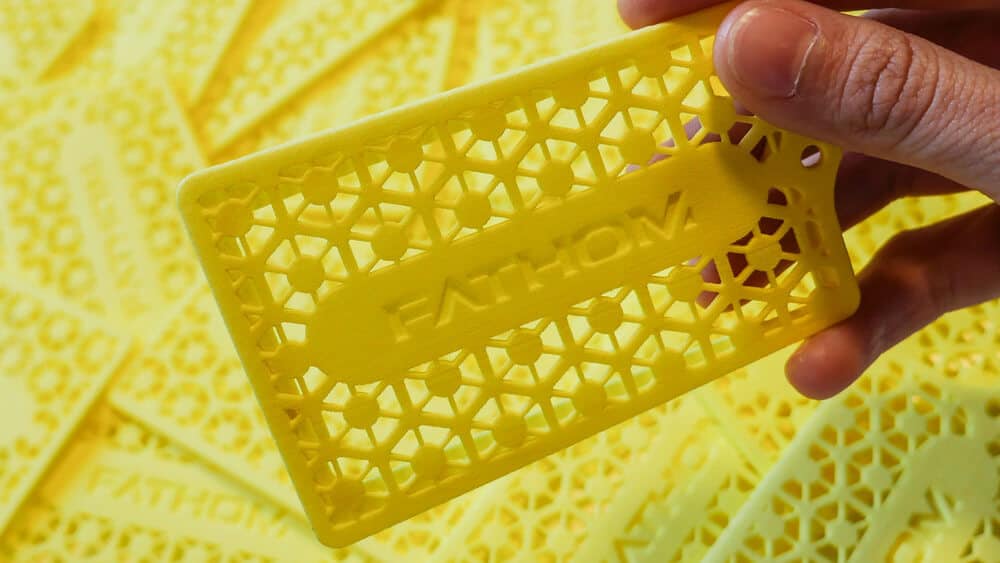
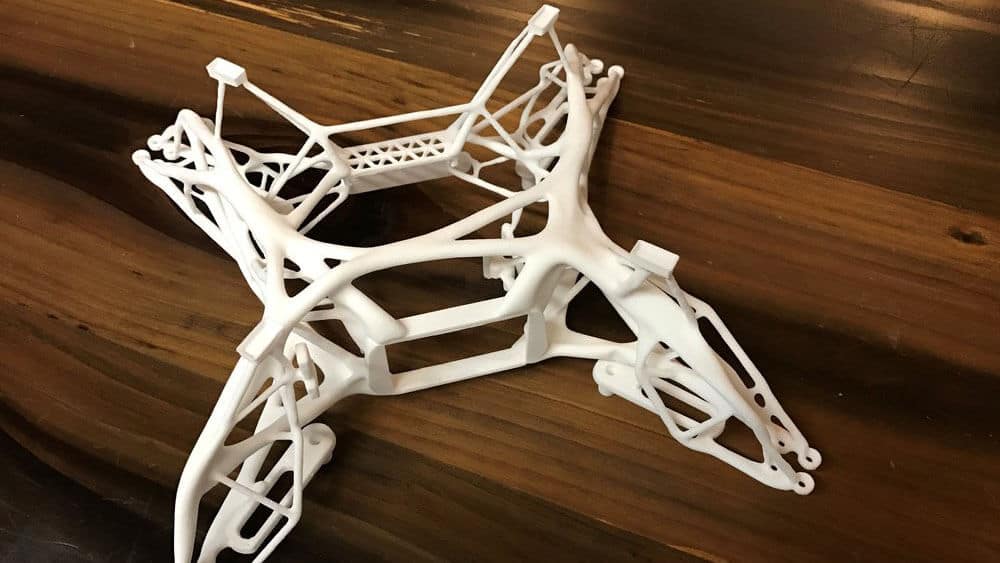
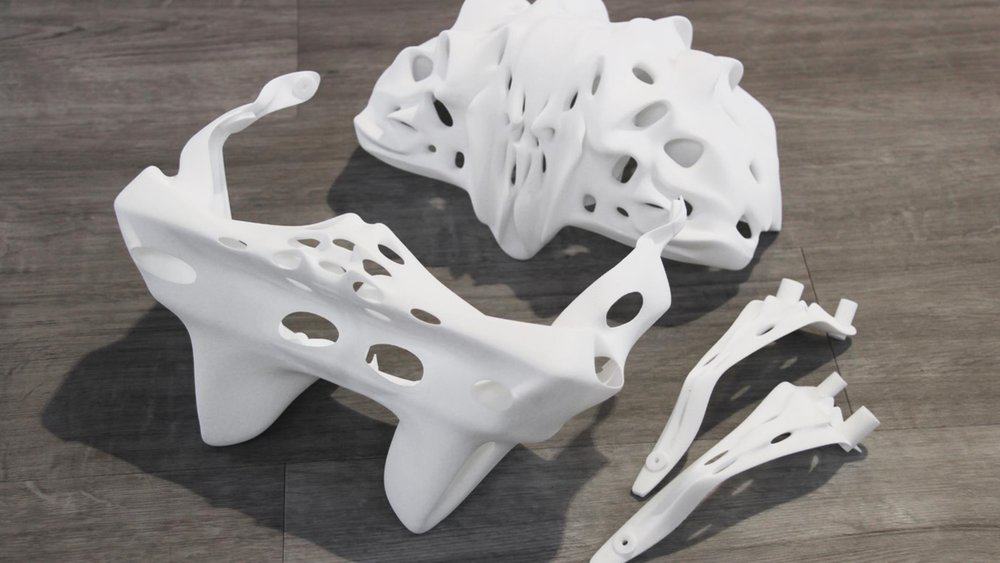
SLS Materials Available / /
Here is a list of materials available for SLS printing with Fathom. Additional materials available upon request.
SLS MATERIALS | LEAD TIME | OPTIMAL QUANTITY | MAXIMUM DIMENSIONS | SUGGESTED MINIMUM WALL THICKNESS | FINISH & APPEARANCE | ADVANTAGES & CONSIDERATIONS |
---|---|---|---|---|---|---|
TPU 88A | 2+ Days | Prototypes, Low-Volume, Short-Run Production | 320mm x 320mm x 610mm | 1mm | Standard Color: White Medium/High Resolution High Detail & Complexity Dye Available (Black, Red, Blue, Green, Orange, Yellow, and Pink) |
High Elasticity, Rebound & Resistance to Fatigue Water-Tight Down to 0.6mm Wall Thickness High Burst Pressure True Thermoplastic Polyurethane With Excellent Flexibility & Durability |
Nylon PA12 (White) | 2+ Days | Prototypes, Low-Volume, Short-Run Production | 320mm x 320mm x 610mm | 1mm | Standard Color: White Medium/High Resolution High Detail & Complexity Dye Available (Black, Red, Blue, Green, Orange, Yellow, and Pink) |
Nearly Isotropic Parts Built Without Supports, Allowing for Complex Geometries Durable Production Quality Thermoplastic |
PA 12 Glass Bead | 3+ Days | Prototypes, Low-Volume, Short-Run Production | 320mm x 320mm x 610mm | 1mm | Standard Color: Off White Medium/High Resolution High Detail & Complexity Dye Available** (Black, Red, Blue, Green, Orange, Yellow, and Pink) |
High Rigidity Resistant To Wear & Tear Thermally Resilient |
PA 11 | 3+ Days | Prototypes, Low-Volume, Short-Run Production | 320mm x 320mm x 610mm | 1mm | Standard Color: White Medium/High Resolution High Detail & Complexity Dye Available (Black, Red, Blue, Green, Orange, Yellow, and Pink) |
High Impact Resistance & Elongation At Break Higher Temperature Resistance Than PA 12 Does Not Splinter Under Load |
PA 11 Fire Retardant | 4+ Days | Prototypes, Low-Volume, Short-Run Production | 320mm x 320mm x 610mm | 1mm | Standard Color: White | High Ductility Combined With Strength Flame-Retardant Properties Are Similar To ULTEMTM Filament |
*Geometry Dependent
**Filled Nylons Can Have Inconsistent Color When Dyed
Nylon is the most common SLS material. Its strength and flexibility make it a popular choice. Polyamide is another common material used in SLS that is strong, flexible, impact-resistant, abrasion-resistant and biocompatible. Carbon-filled Nylon is available upon request
AMT PostPro3D Finishing / /
AMT’s PostPro3D technology is a smart and automated post processing solution for smoothing SLS 3D printed parts. PostPro3D achieves a high quality surface finish that matches injection molding techniques using 3D printing processes. This enabling technology reduces lead-time, cost of manufacture, operational and maintenance costs providing the ‘missing piece’ in the digital manufacturing chain. The PostPro3D machine makes 3D part surface finishing speed and cost competitive for high volume production.
Applications of SLS 3D Printing / /
Designers and engineers across numerous industries have used SLS printing in their product development process. While SLS can be used for prototyping, it is also used for functional parts, testing and production parts. Applications of SLS include //
- Consumer Goods //SLS 3D printing has been used for consumer goods in the medical, footwear and beauty industries.
- Sports //SLS has been used by motorsports companies to innovate vehicle design to increase performance.
- Aerospace // Airline companies are incorporating lightweight SLS 3D parts on their aircraft including air vent grills and other cabin components.
- Tooling Production // Jigs, Fixtures & Other Tooling
- Snap Fits & Living Hinges
- Housings
Advantages of SLS 3D Printing / /
The benefits of SLS include //
- Functional Parts & Prototypes
- No Support Material Needed
- Fast Process
- Parts With Complex Geometries
- Good For Small To Medium Batches
- Good Isotropic Mechanical Properties
- Great For Layer Adhesion
- Reuse Unused Material
- Dye Different Colors
What is the Difference Between SLS & SLA?
Stereolithography (SLA) and Selective Laser Sintering (SLS) are both additive manufacturing processes. SLA is a 3D printing method that uses both a UV laser and a resin that can be cured by UV light. A single laser is directed to specific areas to cure resin and create a solid pattern. SLA is popular because it can print parts with greater precision than traditional Fuse Deposition Modeling (FDM) machines. SLS is another 3D printing process that uses a laser to melt, sinter, or fuse together particles, which result in a 3D printed part. SLS printers are commonly used for plastic, metal and ceramics. These materials are usually in powdered form. SLS does not require support as the unsintered powder around the part provides support. SLS has a broader range of materials available.
There are a number of differences between SLS and SLA. SLS machines use a very powerful laser and as such, they are entirely encased, blocking the view of the part as it is printed. SLA machines are typically enclosed in tinted glass or plastic, which allows the operator to view the part as it is built. SLS does not use toxic resins and the powdered material is considered easier to work with. Objects made by SLA machines are complex and detailed but can be brittle. SLS parts are not as detailed but still complex and are considered suitable for mechanical use.
SLS vs. SLM / /
Selective Laser Melting (SLM), sometimes referred to as Direct Metal Laser Melting (DMLM), uses a laser to melt metallic powders in successive layers. The machine fully melts the powder before another bed of powder is added above the melted layer. SLM causes the metal granules to melt together to fully form one homogeneous piece. The primary difference between SLA and SLS is the material used for each process. SLS can be applied to plastics, glass and ceramics, whereas SLM is used exclusively for metal alloys.
Selective Laser Sintering FAQs / /
Q / / Should SLS Only Be Used For Prototypes?
A //No. SLS parts can be used as production parts.
Q / / What Terms Are Interchangeably Used For Selective Laser Sintering?
A // While selective laser sintering (SLS) is its own unique process, other terms used include 3D printing, SLS manufacturing, SLS prototyping, 3D prototyping, additive manufacturing, rapid prototyping, laser sintering and more.
Q / / During Which Stage Of Product Development Can SLS Be Used?
A // SLS is suitable for any stage of product development, from a functional prototype, to a single-use part, or to create operational pieces.
Q / / Who invented SLS?
A // The SLS concept was originally created in the1980s by Dr. Carl Deckard and Dr. Joe Beaman from the University of Texas and patented in 1988. In 1992, the first industrial SLS printer (DTM Sinterstation 2000) was commercialized. Later, EOSINT P350 by EOS was launched in 1994.
Why Choose Fathom’s SLS 3D Printing Capabilities?
SLS has become popular among designers and engineers for many reasons. SLS allows for higher productivity, lower cost per part and for design flexibility.
- Higher Productivity //Multiple parts can be produced at the same time, which maximizes the build space. The laser used during SLS has a quick scanning speed faster than other processes. Additional parts can be added to the build while it is already in production.
- Lower Cost Per Part //Nylon is the most common material to use for SLS printing and it is one of the least expensive when used in larger quantities. There are additional cost savings since the leftover powder can be reused, support structures are not required, and post-processing in SLS is less labor intensive.
- Design Flexibility //Since SLS does not require support structures, there is an opportunity to produce parts with complex geometries, moving parts and pieces with interior components. SLS is also capable of printing a part that would usually require multiple elements as a single unit. This capability improves the design, saves the design and results in a lightweight part.